ADVANTAGES
- An innovative sustainable solution to moisture-related distresses that is compatible with most water-reducers and air-entrainment materials used in concrete mix design.
- A long-term protection internal waterproofing and moisture blocking for Portland cement concrete (PCC) against water penetration, in all its phases (vapor, liquid and ice).
- A dynamic crystallization system that interacts with water in its three phases which enhances water management (reduced liquid and water vapor movement within the hardened PCC and reduced ice adhesion).
- Reduction in PCC capillary porosity and water permeability (by 2-3 orders of magnitudes).
- Reduced jet fuel and oil penetration through concrete surfaces.
- Hydrophobicity characteristics that help preventing water from wetting and saturating concrete surfaces.
- Reduced ice adhesion and hence reduced consumption of deicing salts & agents.
- Preventing freezing of freshly cast concrete: MCETM has a distinguished and unique thermal behavior of preventing water freezing in MCE-dosed fresh concrete under severe continuous freezing conditions. Figure 1 shows that the temperature of MCE modified fresh concrete remained above freezing temperature for about 2 months (when the concrete is continuously subjected to -50oF), while the temperate of the control sample dropped to a value below freezing within three days.
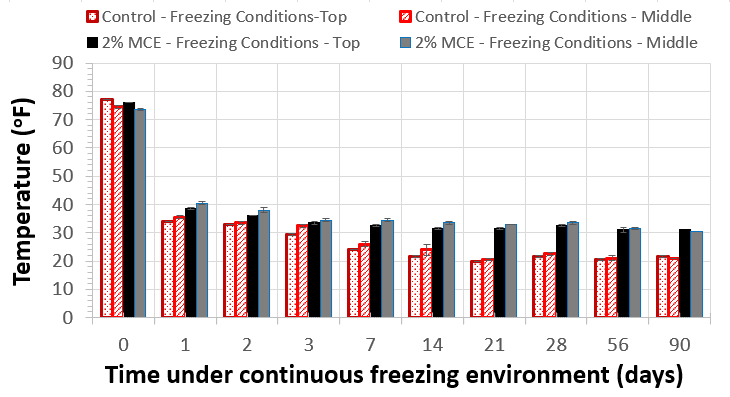
Fig. 1: Concrete thermal performance under continuous freezing environment, reporting the temperatures at two positions: top (0.5 inch below surface) and middle (1.5 inch below surface) for a concrete with a mix design of IDOT C4, comparing control sample with concrete mixed with 2% MCETM. The tests were made in freezing chambers used for ASTM C-666, with the temperature of the chamber adjusted to -50oF and remained constant to create more severe freezing conditions.
- Improved freeze-thaw durability. Experimental data of IDOT C4 mix concrete samples with 2% MCETM indicate a reduction of mass loss by 91.6% and an increase in the relative dynamic modulus by 20.3%. The results of % mass loss presented in figure 2 are from an independent laboratory testing according to ASTM C 666.
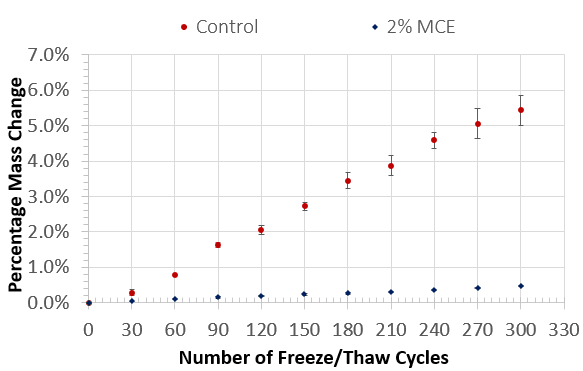
Fig. 2: Increasing resistance to freeze thaw cycles with MCETM at 2% of cement weight. According to ASTM C 666 using IDOT C4 PCC mix.
- Reduced chloride ion penetration from deicing salts, increased concrete electrical resistivity by a percentage over 90% and reduced associated steel corrosion and paste degradation.
- Reduced Alkali Silica Reactivity (ASR) problems and silicate dusting: The percentage reduction in length change due to ASR in 2% MCE- dosed concrete including reactive aggregates can be in the range of 45-77% (according to ASTM C1567, 28 days testing). Fig. 3 shows that MCETM meets the requirement of ASTM C1293 (long term testing) by not going above the 0.04% ASTM limit (for one year), see Fig. 3.
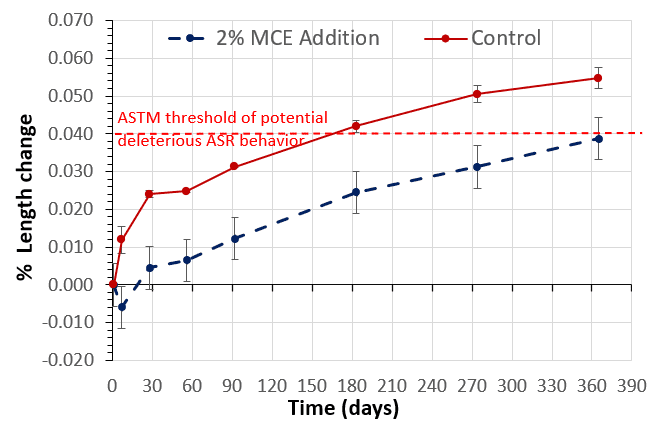
Fig. 3: The results of the long-term ASR experiments using the concrete-prism (ASTM C1293) for reactive coarse aggregates showing results for control specimens made with reactive coarse aggregates of Knife River compared to those for MCE-Dosed specimens. The standard errors of the replicates are shown as error bars. Also shown is the ASTM threshold indicative of potential deleterious ASR behavior (dashed line).
- Reduced fungal and microbial growth according to anti-fungal and microbial test method MIL-SDD810G (reduced mold associated problems).
- Enhanced workability and finishability: the effective compounds of MCETM enhance concrete slump as indicated in fig.4. The results in Fig. 4 are for concrete mix designs with and without fly ash, obtained by an independent laboratory testing
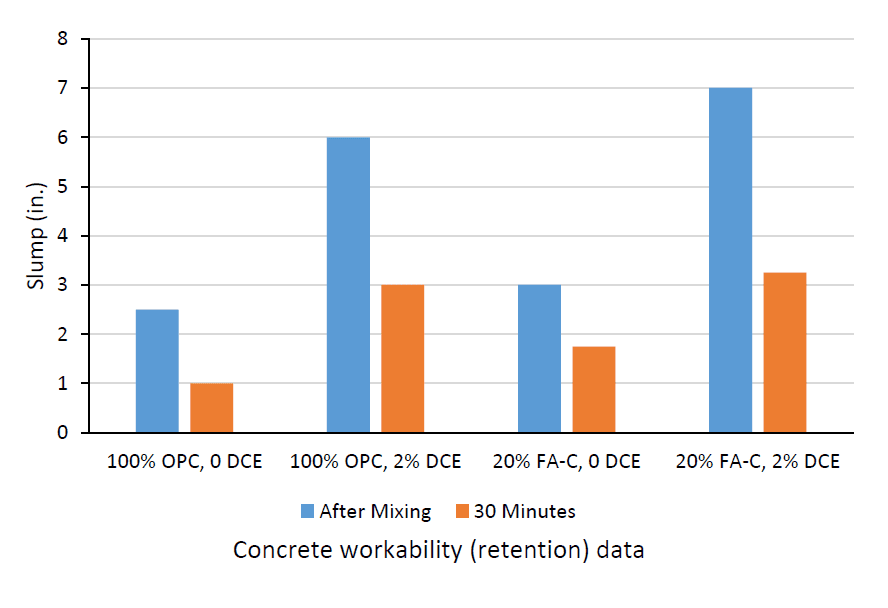
Fig. 4: Enhanced workability and retention of concrete with 2% MCETM
- Reduced shrinkage and surface cracking.
- Helps concrete stay whiter & brighter (Albedo Surface).
TECHNICAL
Physical Properties
Specific Gravity |
1.1 – 1.2 |
Viscosity |
2.4 centipoises |
Freezing Point |
24ºF (-4.4°C) |
Boiling Point |
219ºF (104 °C) |
Color |
Clear |
Environmental Hazards |
None |
Odor |
None |
Toxicity |
None |
Fumes |
None |
Flammability |
None |
Product Performance is tested according to the following test standards:
- CRD-48-92 US Army Corps of Engineers Standard Test Method for Water Permeability of Concrete
- ASTM D6489-99 Determining the Water Absorption of Hardened Concrete Treated with a Water Repelling Coating.
- ASTM C642-97 Standard Test Method for Density, Absorption, and Voids in Hardened Concrete.
- ASTM C642-97 Density, Absorption, and Voids in Hardened Concrete.
- ASTM C1202-91 Electrical Indication of Concrete’s Ability to Resist Chloride Ion Penetration.
- AASHTO T260 Sampling and Testing for Chloride Ion in Concrete and Concrete Raw Materials.
- AASHTO T277 Electrical Indication of Concrete’s Ability to Resist Chloride Ion Penetration.
- AASHTO T259-00 Resistance of Concrete to Chloride Ion Penetration.
- ASTM C1218 Water-Soluble Chloride in Mortar and Concrete.
- ASTM C672-98 Scaling Resistance of Concrete Surfaces Exposed to Deicing Chemicals.
- ASTM C457-98 Microscopical Determination of Parameters of the Air-Void System in Hardened Concrete.
- MIL-STD-810G Fungal Resistance According to Test Method Standard for Environmental Engineering Considerations and Laboratory Tests.
- ASTM D7234 Pull-Off Adhesion Strength of Coatings on Concrete.
- ASTM D4541-95 Pull-Off Strength of Coatings Using Portable Adhesion Testers.
- ASTM C1583 Bond Strength or Tensile Strength of Overlay Materials by Direct Tension.
- ASTM F609-96 Standard Test Method for Using a Horizontal Pull Slipmeter (HPS).
- ASTM E303-93 Measuring Surface Frictional Properties Using the British Pendulum Tester.
- ASTM D7234 Standard Test Method for Pull-Off Adhesion Strength of Coatings on Concrete Using Portable Pull-Off Adhesion Testers.
- ASTM C666-97 Resistance of Concrete to Rapid Freezing & Thawing.
- ASTM C1567 Standard Test Method for Determining the Potential Alkali-Silica Reactivity of Combinations of Cementitious Materials and Aggregate (Accelerated Mortar-Bar Method).
- ASTM C1293 Standard Test Method for Determination of Length Change of Concrete Due to Alkali-Silica Reaction.
APPLICATION
Method of Application: MCETM is shipped in a ready-to-use state, with no additional preparation prior to use. The product is simply mixed with the concrete at the time of batching and is applicable to both ready-mixed and central mix production.
Blending: The MCETM can be introduced into the water stream at the time of batching or added to fresh concrete mixture at the job site.
Consumption: recommended at a typical dosage of 2% by weight of cementitious materials.
Cleaning: clean all equipment and tools with fresh clean water immediately after use.
STORAGE
Two years shelf life when stored in a cool, dry place in its original unopened container. Always agitate or stir the product’s container before using it. DO NOT ALLOW THE PRODUCT TO FREEZE. Repeated freezing & thawing might cause damage to the product.
SAFETY
As with all construction chemical products, adequate precautions and care must be taken during usage and storage. Avoid direct contact with foodstuff, eyes, skin, and mouth. Any direct contact with skin, eyes, etc. should be washed thoroughly with clean running water and soap.
Always wear protective goggles and gloves. In case of eye contact, flush for 15 minutes with warm water. KEEP OUT OF REACH OF CHILDREN.
WARRANTY
LIMITED WARRANTY: International Chem-Crete Inc. warrants that, at the time and place we make shipment, our materials will be of good quality and will conform to our published specifications in force on the date of acceptance of the order.
DISCLAIMER: The information contained herein is included for illustrative purposes only and, to the best of our knowledge, is accurate and reliable. International Chem-Crete Inc. is not under any circumstances liable to connection with the use of information. As International Chem-Crete Inc. has no control over the use to which others may put its products, it is recommended that the products be tested to determine the suitability for specific applications and/or our information is valid in particular circumstances. Responsibility remains with the architect or engineer, contractor and owner of the design, application, and proper installation of each product. Specifier and user shall determine the suitability of the product for a specific application and assume all responsibility in connection therewith.
NO OTHER WARRANTIES EXPRESS OR IMPLIED SHALL APPLY INCLUDING ANY WARRANTY OF MERCHANTABILITY OR FITNESS FOR A PARTICULAR PURPOSE. CHEM-CRETE SHALL NOT BE LIABLE UNDER ANY LEGAL THEORY FOR SPECIAL OR CONSEQUENTIAL DAMAGES. CHEM-CRETE SHALL NOT BE RESPONSIBLE FOR THE USE OF THIS PRODUCT IN A MANNER TO INFRINGE ON ANY PATENT OR ANY OTHER INTELLECTUAL PROPERTY RIGHTS HELD BY OTHERS. MJ17922-1